Сотовый поликарбонат – универсальный материал в виде полимерных листов с ячеистой структурой. Наличие сот между слоями обеспечивает дополнительную жесткость. Толщина изделий варьируется в пределах 4-32 мм. Цветовая палитра материала насчитывает более 15 расцветок. Поликарбонатные листы активно используются в отделке, строительной сфере, сельском хозяйстве и при изготовлении рекламных конструкций. С помощью полимерного материала создают арки, навесы, ограждения и витрины.
Сырье для сотовых поликарбонатных листов
В качестве материала для производства сотового поликарбоната задействуются органическое сырье. Бесцветные гранулы состоят из аморфного инженерного пластика, угольной кислоты и двухатомного фенола. Благодаря сложному составу с множеством компонентов поликарбонат приобретает следующие свойства:
- большой запас прочности;
- устойчивость к перепадам температуры;
- гибкость;
- малый вес;
- отличные теплоизоляционные показатели;
- негорючесть;
- длительный срок эксплуатации (до 20 лет).
Для продления идеально внешнего вида поликарбонатных листов их поверхность может покрываться специальным защитным составом против ультрафиолетовых лучей.
Особенности производства материала
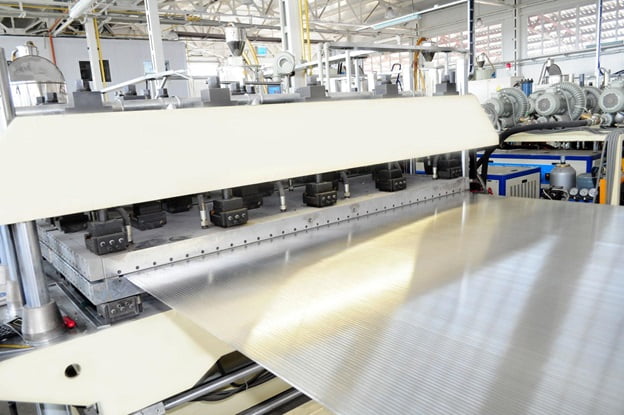
Для изготовления сотового поликарбоната задействуется экструзионная линия. На начальном этапе производства гранулы фасуются и направляются на плавку. Чтобы придать листам нужный цвет, добавляется краситель. Затем осуществляется процесс расплавления сырья. Гранулы находятся в специальной камере, где нагреваются и переходят в текучее состояние. На этом этапе в массу добавляют различные компоненты, повышающие эксплуатационные характеристики готовой продукции. Затем листы подвергаются формировке. Расплавленная масса поступает в агрегат с целью формирования требуемой структуры. Как только остынет материал, осуществляется отсечение листов разных размеров. После этого они фасуются.
Пластик поликарбонат получают за счет синтеза, который включает в себя несколько стадий и разные компоненты. На производство сырье поступает расфасованным во влагостойкие мешки. Гранулят взвешивается и направляется на хранение в силос. Для производства материала может задействоваться белый, цветной или бесцветный гранулят.
Очистка и плавление гранул
Из высоких складов гранулы по пневматическому транспортеру поступают в циклон (приспособление, имеющее вид центрифуги). Здесь сырье подвергается очистки от пыли, мусора и разных примесей. Важно устранить любые посторонние примеси, так как они могут негативно отразиться на качестве готовой продукции и ухудшить прозрачность. Обеспыленные гранулы проходят через автоматический дозатор и направляются в специальную камеру для плавления. С помощью добавок поликарбонатные листы могут отталкивать грязь и влагу. Добавление металлической крошки придает материалу благородный оттенок, но и позволит листам отражать инфракрасный свет. Поликарбонатная смесь нагревается до 250-290°C и приобретает однородный вид. Образовавшиеся газы отводятся наружу.
Процесс экструзии
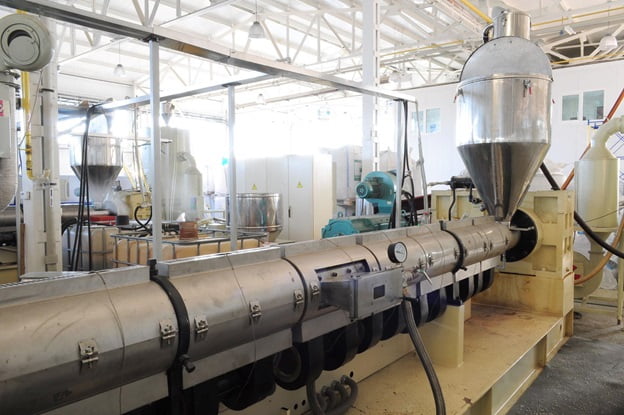
Каждая производственная линия, на которой изготавливаются листы сотового поликарбоната, оснащается экструдером. В данном оборудовании формируется сотовая структура материала. Высоковязкое вещество проходит через специальную матрицу/фильеру. В результате получается изделие требуемого профиля. Соэкструзия тонкой пленки обеспечивает поглощение ультрафиолета. Данный вид защиты гарантирует материалу во время эксплуатации неизменность первоначальных оптических свойств и высокую прочность. Поликарбонатная лента прессуется, что позволяет получить нужную толщину и гладкую поверхность.
Нарезка и контроль качества
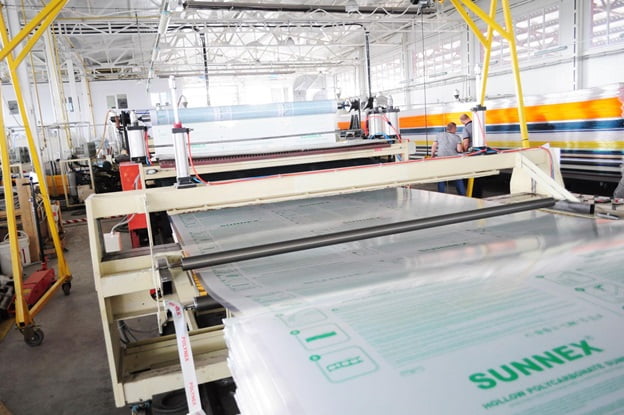
При остывании лента приобретает естественную форму. Затем ее нарезают на листы. С помощью специальных ножниц аккуратно обрезается кромка, а затем выполняется поперечная нарезка. Стандартным размерам являются: длина 12 м и ширина 2.1 и 6 м. При потребности листы могут изготавливаться по индивидуальным параметрам. Готовая продукция укладывается на поддон. Каждое изделие подвергается тщательному внешнему осмотру на наличие брака. За счет специального устройства производится проверка толщины, прочностных характеристик, уровня светопропускаемости, а также защитного слоя против ультрафиолета. После прохождения контроля качества готовая продукция отправляется на склад, а затем отгружается конечному потребителю.